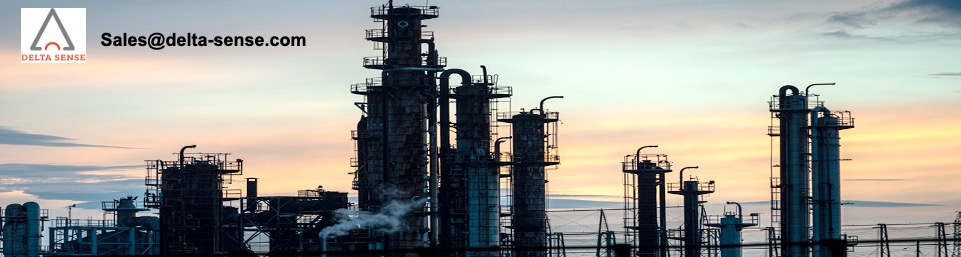
|
Home |
Products |
Company |
About us |
Continuous Emission Monitoring (CEMS)
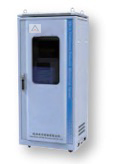
|
Gas & Odor Detection System
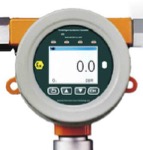
|
Air Quality Monitoring (AQMS)
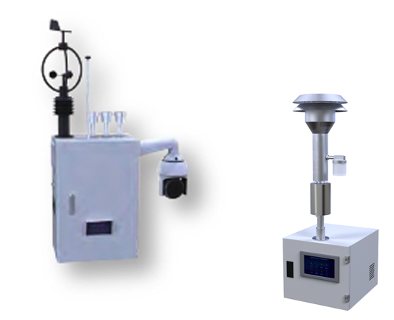
|
- 1.1 Continuous Emission Monitoring System
- 1.2 Gas Analyzer
- 1.3 Stack Flow Meter
- 1.4 Dust Analyzer
|
|
|
1.1 Continuous Emission Monitoring System CEMS
Continuous Emission Monitoring & Process Control
The instruments and analyzers produced by one of the best continuous emission monitoring system suppliers, Delta Sense now are widely used at home and abroad. They are: IR and UV DOAS gas analyzer, laser TDLAS gas analyzer, forward/backward laser dust monitoring devices, hygroscope for high temperature, continuous emission monitoring system (CEMS), denigration escape ammonia analyzer, Sulphur analyzer, immersive UV broad spectrum water analyzer, ammonia nitrogen analyzer, colorimetric heavy analyzer, anodic stripping voltammetry heavy metal analyzer etc.
Delta Sense, as one of the most professional CEMS analyzer manufacturers, has cooperated with and attracted many worldwide clients of online gas analysis and process control, including system integrator, agents, operation and maintenance providers, CEMS equipment manufacturers, thermal power plants, sewage treatment plants, chemical plants and the like.
Types of CEMS Analyzer >>
|
1.1.1 GS3000 CEMS Extractive Gas Analyzer UV/IR CEMS
|
1.1.2. DGT-450 In-situ (Semi) CEMS
DGT-450 Flue Gas Analyzer is a highly integrated single-flange gas monitoring equipment, of which, core detection module adopts Tunable Diode Laser Absorption Spectroscopy (TDLAS) and Differential Optical Absorption Spectroscopy (DOAS) gas absorption technology with independent intellectual property rights. The specially designed measuring cell effectively improves optical path length for gas absorption, which can measure trace gas accurately inside pipeline
DGT-450 can be widely applied in online gas monitoring occasions including denitrification device, boiler flue and exhaust detection, etc. One equipment can realize online monitoring for multiple gas components, such as CO, CO2 , SO2, NO, NO2 and O2 etc
|
1.2 Gas Analyzer
|
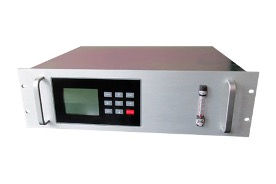
GS-5000 continuous online flue gas analyzer is a series of self-developed gas analysis products for online gas analysis to environmental protection and industrial control. Based on UV Differential Optical Absorption Spectroscopy (DOAS) technology and chemometrics algorithm (PLS), our online gas analyzer is able to measure the gas concentration of SO2, NO, NO2, O2, NH3, Cl2, O3, H2S, Ch3, O2
etc.
|
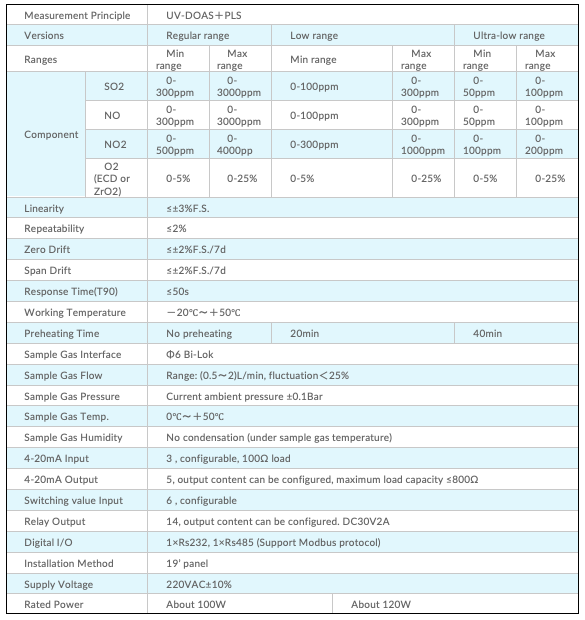 |
1.3 FPT-500 Stack Flow and Temperature Meter
|
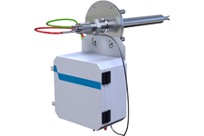
The temperature pressure & velocity integrated monitor is based on pitot differential pressure velocity measurement principle. During measurement, insert the probe of pitot tube into pipeline and make the direction of probe dynamic hole face the flow direction directly and static hole back to the flow direction. Transfer dynamic pressure and static pressure to pressure transmitter respectively and then calculate velocity value according to formula.
When measuring differential pressure, differential pressure transmitter is required to measure both dynamic pressure and static pressure. Thus, special attention shall be paid to the direction of pitot tube during installation, making sure both pressure-acquiring ports are consistent with the flow direction of flue gas (dynamic pressure measurement port is required to align with coming direction of flue gas while static pressure measurement port aligns with the departure direction of flue gas). There are two installation methods, vertical type and horizontal type, as shown in the following figure.
|
Feature of Stack Flow and Temperature meter
- Low range pressure sensor to realize 1m/s flow velocity measurement
- Operation unit with LCD display: provide friendly human–machine interaction interface
- Able to set regular purging time, velocity field parameter, pitot coefficient and etc.
- Overvoltage protection to effectively prevent pressure sensor from damage and reduce operation cost
- Automatic zero calibration; strengthen output signal
- Anti-blocking and anti-corrosion design
- High accuracy, small impact and simple pipeline design
- Able to measure pressure of purging gas and determine if there is gas pressure
|
1.4 Dust Analyzer
|
1.4.1 DPS-100 Dust Monitoring System
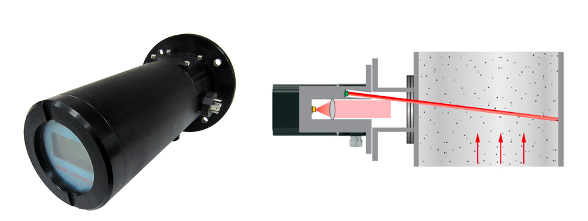
The DPS-100 dust particle measuring device consists of the optical part, circuit and signal processing part, calibrator and air curtain protection part.
The laser beam (650nm) emitted by semiconductor laser enters the stack and produces scattering light by interaction with dust particles. The backscattered light of the DPS-100 dust particle measuring device enters the photosensitive detector through the convergence of the lens. The signal processing circuit converts the light signal into a standard signal in proportion to dust concentration and output, thus dust particle emission concentration of pollution source is obtained.
|
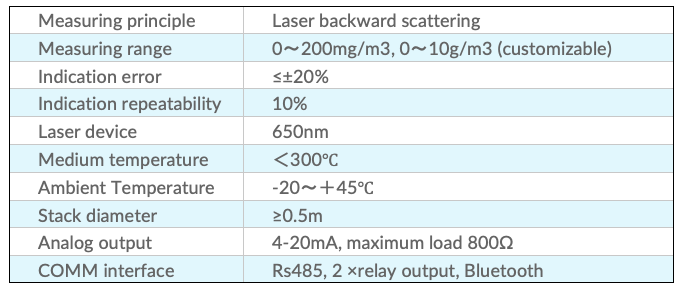 |
1.4.2 DPS-200 Dust Monitoring
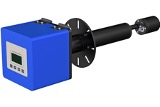
• Adopt the laser forward scattering method to measure dust concentration; the lower detection limit is as low as 0.05mg/m3
• Employ gas curtain purging to protect laser and lens of detector end; purging gas is automatically heated by the temperature of the stack inside feeler lever and achieve positive pressure dust prevention inside feeler lever
• High-temperature resistance design of the probe part
• Automatic zeroing and calibration of the double optical path
• Support manual range calibration
• Support automatic range calibration
|
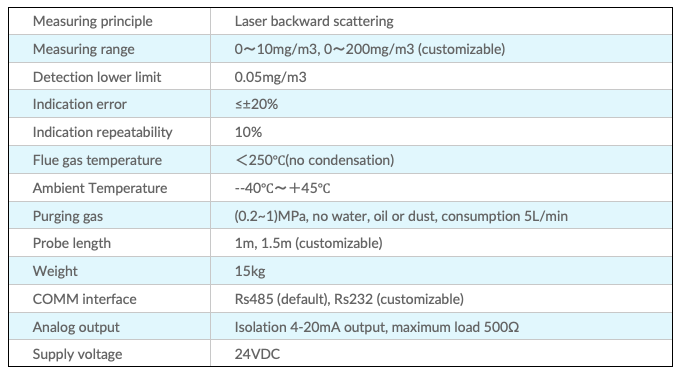
|
delta-sense© 2025. All Rights Reserved |